FRP Fan stack is also known as Fan ring, Fan Cylinder and Fan Shroud
What is fan stack or fan ring
Fan stack is a boundary around the fan to separate air inlet and air delivery. According to ASHRAE guidelines, proper fan stack design is essential for optimal cooling tower performance and energy efficiency.
It has three main components fan cylinder or fans cashing, air inlet or inlet bell, and fan diffuser or velocity recovery cone.
Fan stacks used for the following function
- It maximizes fan efficiency.
- It reduces sound levels near the fan system.
- Stack prevents the reverse running of the fan due to external air interference.
- The Inlet bell provides smooth airflow to the fan.
- The Inlet bell also restricts vena contracta at the fan inlet.
- Fan stack also minimizes discharge air recirculation.
We are a manufacturer of FRP fan stack. Our fan fan flues have designed for the smooth surface finish on the working part as well as having superior strength.
In some fan systems, individual components of the stack used alone or with each other.
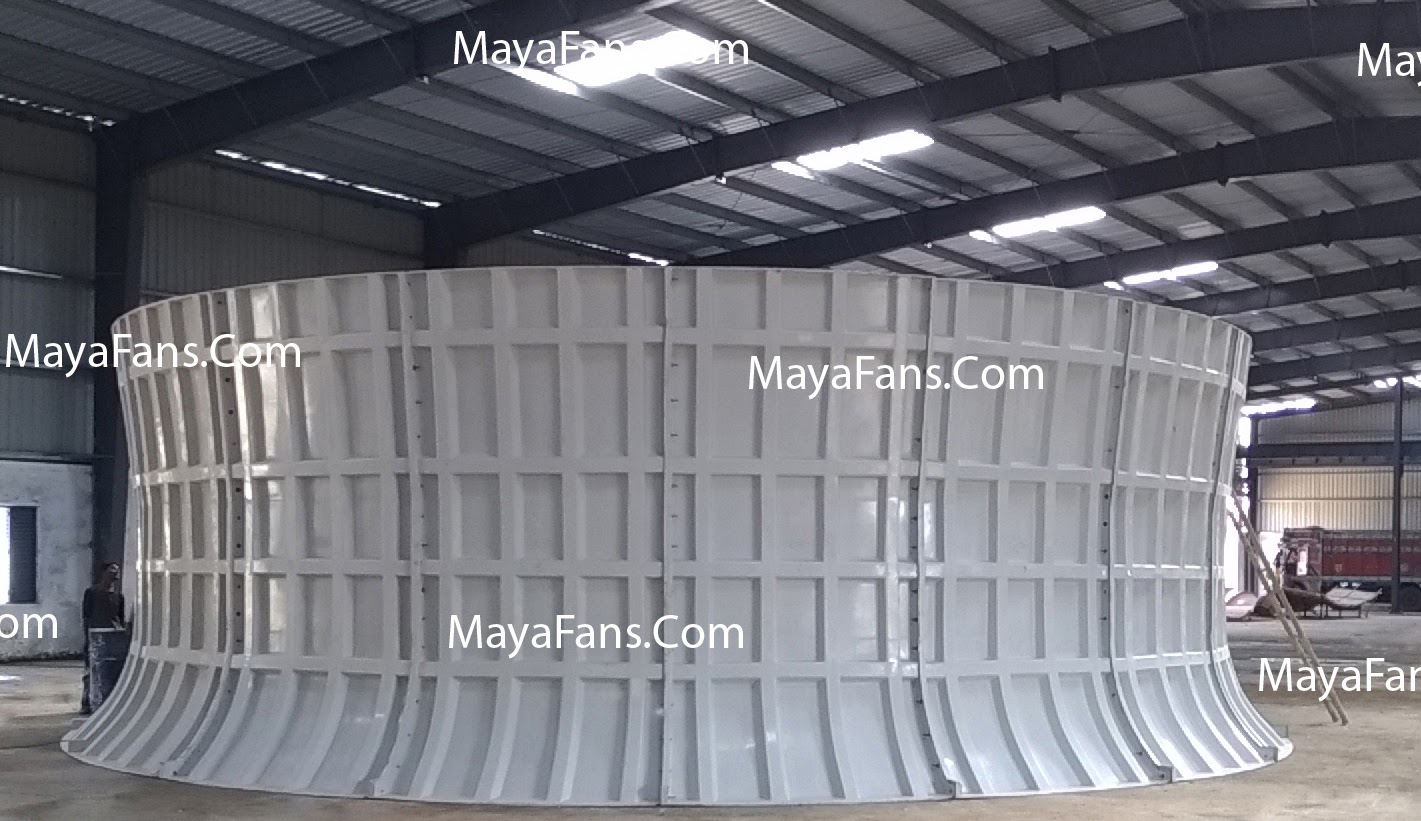
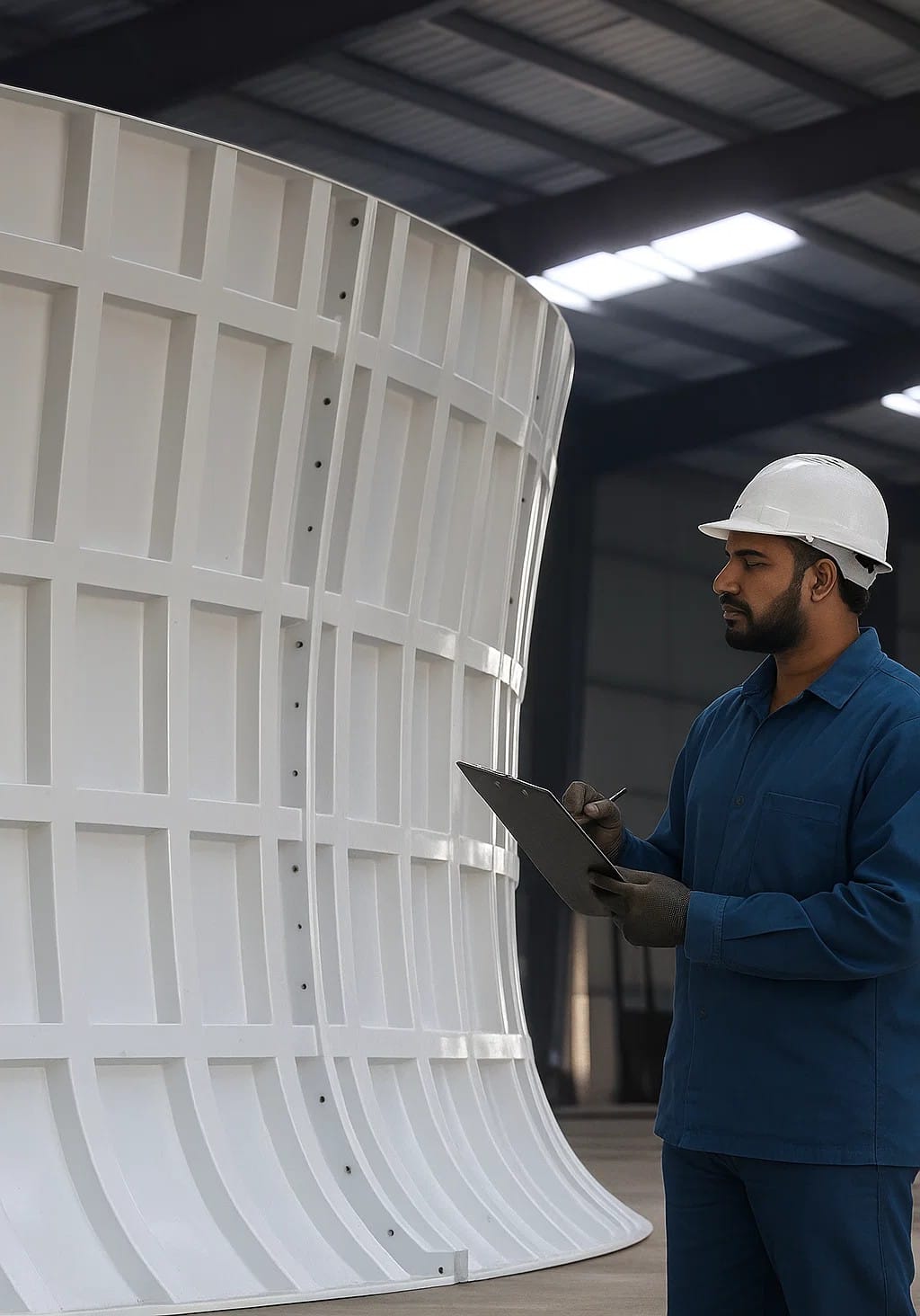
Key components Fan Stack System

Fan Cashing (Fan Ring)
it is the portion where fan operate it has to be there in all case.
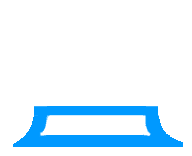
Air Inlet Bell
It used to ease smooth air entry to the fan.
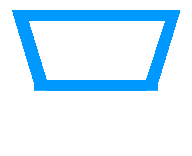
velocity Recovery Cone
It is a conical cylinder of gradually increasing diameter at the fan exit.
Stack Diamater Range Up To
Stack Height range up to
7 Features of the MAYA Ultimate FRP Fan Stack
- Our Fan Cylinder enables high velocity-recovery efficiency that meets CTI certified performance standards. This improves system efficiency and reduces operation cost while ensuring compliance with industry benchmarks.
- Fan Shroud manufactured from high-quality fibreglass-reinforced plastic that meets international composite material standards and industry quality specifications.
- Maya fan offer fan flues in all type of finish, inside finish, outside finish, and double-finish design. for more detail please
- The smooth inner surface of fan stack drops friction losses. Which provide laminar airflow and reduce turbulence.
- outer surface provides high resistance against climatic conditions.
- High-quality UV protection on both the surface prevents UV rays hamper the stack life.
- Fiber fan stack is reliable yet less in weight. This contributes to improving the cooling tower life.
In some case fan flues of an extended height required, to promote the discharge of the saturated airstream at higher elevations. It minimizes the effects of recirculation and interference.
The cooling tower fan stack is also known as a cooling tower fan shroud and cooling tower fan cylinder.
Fan Stack is an essential part of the system manufactured from fibre-reinforced plastic (FRP).
Fan Stack is a common term in cooling tower industries for the combination of three components of airflow path it includes-
- An air inlet is also known as fan bell or bell inlet.
- Fan casing the part in which fan operate this is also known as fan cylinder, fan shroud and fan ring.
- The third part of the stack is a velocity recovery cone. It used to recover velocity pressure with the help of a conical divergent at fan exit this also known as fan diffuser.
These stacks have vertical and horizontal ribs which make it very strong to sustain in high wind velocity conditions. We have the in-house capability to develop pattern and mould, so we make any size of fan cylinder, and it manufactured in assembled segments.
Fan Air Inlet/ Inlet bell / Fan Bell
In the fan system, the air behind fan come from large volume and have to pass through a small cross-section of the fan casing.
Therefore fan develops negative pressure behind the fan, this pressure is equal in all direction, so it sucks air from every direction.
This air moves toward the fan radially on the smallest distance path. Thus, some of the air move perpendicular to the axis of the fan.
Due to inertia of air coming other than axial direction so resultant air bend toward the centre of cashing and create Vena contracta.
It is like the picture at right having visible vena contracta at a canal.
These phenomena remain much more severe in fans as the velocity of air in fan is much higher, thus it impacts the fan performance.
So to ease the smooth transition of air at fan inlet different shapes utilized to reduce the losses these known as Fan air inlet, inlet bell or fan bell.
This inlet bell provides:-
- Uniform flow at inlet.
- Lower fan noise.
- Reduce Turbulence.
- Reduce pressure drop and horsepower
- And increase airflow at the same fan power.

North Karanpura Super Thermal Power Project – Maya Fan is a proud Partner of India’s Largest ACC fan ring supply
At a project of National thermal power corporation (NTPC) which is India’s largest power producer. This handled by the Bharat Heavy Electrical Ltd (BHEL) one of the government giant for EPC project. And ACC of the project supplied by Harbin Air conditioning (HAC)
- The first time NTPC is using ACC for the power plant.
- It is India’s Largest ACC and maybe Asia’s Largest.
- The project having 3 unit of 90 cells.
- FRP axial Fan size is 36 foot.
Not only supply fan ring, but we also supplied the fan guard for as well as at NTPC in NKP Project Summery
You can know more about this project at – Gem Wiki and to know more about project please visit NTPC North Karanpura Super Thermal Power Project Project summery document.
Fan ring and Guard
Single Projects Supply
Types of fan air inlet

FLANGE INLET
Most of the time casing with flange and in some cases an extended piece provided to allow some extra distance for air equalization.
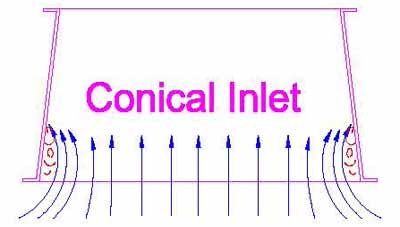
CONICAL INLET
A conical shape added which increase effective inlet area but the disadvantage of flange inlet still exist
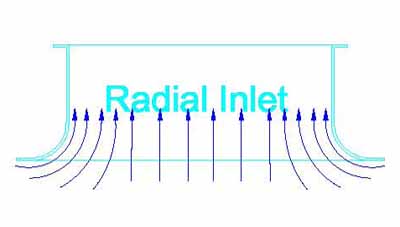
RADIAL BELL
It is a most used inlet type and having a very good advantage on system.
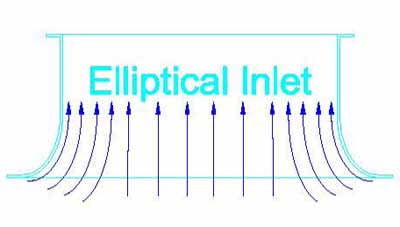
ELLIPTICAL BELL
It used in cooling tower and mining industries have a very good effect of flow guiding and equalization.
Fan casing
It is the boundary which shrouded around the fan and cylindrical in shape, so, it is also known as fan cylinder or fan ring.
It is the most important part which partition +iv and –iv pressure plain.
Back of fan is suction side it is –iv pressure plane of fan and front or delivery side is +iv pressure plain.
The casing should be as accurate in shape as possible because in case of any irregularity it can cause vibration and may develop fatigue on the fan blade.
It is very important to maintain least tip clearance which is a space between the blade tip and casing, as this is the place where two different pressure plane come in contact thus air tends to move back from +iv pressure to –iv pressure side.
So it is always preferable to maintain the smallest and uniform tip clearance and It should be less then 1% of diameter.
Also, the problem of tip clearance become more critical with increasing static pressure in the fan.
With increasing tip clearance efficiency of a low-pressure fan spoiled up to 20 % and high-pressure fan will get stalled and the air starts circulation from this space.
We provide:-
- Heavy-duty robust integrated casing for mining fans.
- FRP cashing for OEM of cooling tower and ACC.
- Fan shroud/ring in combination with inlet bell, delivery diffuser or both.
DIFFUSER / VELOCITY RECOVERY CONE
In general, a significant amount of effort made by the equipment is wasted in exit air energy. The system draws air and delivers it to the environment at atmospheric pressure (at zero pressure).
So velocity recovery cone, which is a conical cylinder of increasing diameter, is an ideal tool to cut this exit air velocity. This utilizes the largest amount of dynamic pressure recovery into static pressure regain. The energy of air at any point of the system remains the same. Thus energy at the equipment and energy at exit is same – only some losses in the path from equipment plane to the exit plane happen, so it can be derived as:
Technical Calculations:
Psf + Pvf = Pse+Pve+ L Psf = Pve – Pvf + L
Where:
- Psf = Static pressure at equipment
- Pvf = Velocity or dynamic pressure at equipment
- Static pressure at diffuser exit is zero (Atmospheric pressure)
- Psf = Velocity pressure at diffuser exit
- L = losses (common rule of thumb is 70% of the difference in velocity pressure (Pve – Pvf) recovered in recovery cone portion of the cylinders)
In actuality, this percentage may vary from 50% to 95%, depending on operating conditions and diffuser quality (i.e., shape consistency and finish of inner surface). Since the velocity of discharge air stream reduces at the exit of the diffuser, Pve is less than Pvf. This means that relative to atmospheric pressure, static pressure at a point just above the equipment plane becomes more negative by adding recovery cone.
So by adding velocity recovery cone, pressure against which the equipment operates is reduced compared to no use of velocity recovery cone. This is a significant advantage and improves system performance to a great extent. With the use of velocity recovery cone, the same air can be delivered at much lesser power consumption. Or with the same power, a higher quantity of air can be delivered.
A diffuser converts dynamic energy into static pressure. Thus higher the exit air velocity, the greater advantage of velocity recovery cone can be achieved.
In different applications, velocity recovery cones used are different. It depends on installation conditions and exit air quality. Like in cooling towers, it remains part of the assembly and is constructed in combination with casing and air inlet. Also, as this diffuser has to deal with humid air, it is mostly constructed with materials like wood, concrete and FRP.
In cooling towers, long diffusers also help in the prevention of plume recirculation by delivering it at a higher elevation. In mine ventilation, diffusers are mostly made of steel and very long as they handle high-speed air and have high dynamic pressure.
Types of Finish for FRP Fan Stacks:
Inside , Outside, and Both-Side Finish Options
When choosing an FRP fan stack for cooling towers, air-cooled condensers, or industrial ventilation systems, the surface finish—inside, outside, or both-side—significantly impacts performance, protection, and maintenance –
Both-Side Finish
An inside finish model features a smooth interior surface that improves airflow, reduces turbulence, and enhances efficiency while helping lower operational noise. Though this type offers limited protection on the exterior, Maya Fan addresses this by applying an extra UV-protective layer on the outer surface, improving weather resistance and extending product life.
An outside finish variant, on the other hand, emphasizes external durability with robust UV, corrosion, and weather protection—making it ideal for exposed environments—though it may slightly compromise internal airflow efficiency.
For maximum benefit, a both-side finish FRP unit combines the internal smoothness of an inside finish with the rugged protection of an outside finish, offering optimal performance and long-term durability. However, this option involves a significantly higher cost due to the additional processes involved.
We focus on practical outcomes—airflow optimization, corrosion resistance, and lifecycle value—when guiding customers toward the best FRP assembly, ring, or cylinder for their system.
FEW OF OUR PRESTIGIOUS CUSTOMER



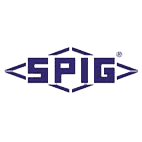
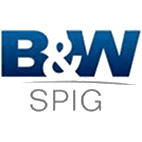

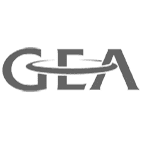
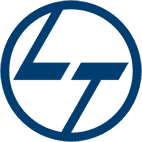
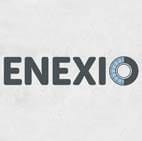

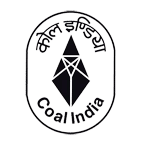

❓ Frequently Asked Questions – FRP Fan stack
What is a fan stack (also known as fan ring or fan cylinder)?
A fan stack is an assembly comprising the inlet bell (fan bell), the cylindrical casing that encloses the fan, and a velocity-recovery cone or diffuser. It plays a crucial role in cooling towers and ACC systems, designed to:
Smooth airflow and reduce turbulence
Enhance static efficiency, cutting power costs
Lower noise levels
Prevent reverse airflow and air recirculation
What materials and finishes are used in Maya FRP fan stacks?
Maya fabricates fan stacks from 100% fiberglass-reinforced polyester (FRP). They feature:
Dual-surface finish: a smooth internal layer for laminar flow and a UV-resistant external layer
Lightweight yet robust construction, outperforming heavier materials like concrete
What efficiency gains can I expect with an FRP fan stack?
Maya’s FRP fan stacks can improve energy efficiency by 15–40% by reducing friction and recovering velocity pressure. Better laminar flow means less turbulence, lower power draw, and significant cost savings.
How does a velocity recovery cone (diffuser) help fan performance?
By gradually expanding the outlet area, the cone converts dynamic pressure to static pressure—recovering up to 50–95% of velocity pressure. This lowers the fan’s backpressure requirement, enabling higher airflow or reduced power consumption.
What range of sizes do Maya FRP fan stacks support?
Fan stacks are available in diameters ranging from 10 ft to 58 ft (approx. 3–16 m), with many built in modular sections for easy assembly and ship-to-site installation.
Can I order fan stacks customized to my specifications?
Yes. Maya offers fully customizable fan stacks—including inlet bells, casings, and diffusers—based on customer drawings or specs. They support both FRP and metal builds, with in‑house tooling and fabrication facilities.
Why choose FRP over metallic or concrete stacks?
FRP offers:
High corrosion and chemical resistance—ideal for wet or chemical-laden air
Ease of handling and installation due to lightweight
UV protection and durability even in harsh conditions
Excellent performance vs cost balance
How do inlet bells reduce fan power and noise?
Inlet bells guide and equalize airflow entering the fan, reducing vena contracta and turbulence. This leads to:
Lower noise
Reduced pressure drop
Decreased horsepower demand
Does a fan cylinder (casing) matter for efficiency?
Absolutely. The casing maintains tight clearance (< 1% of blade tip) to prevent airflow leakage. Irregularities or excessive clearance can degrade efficiency up to 20%, or even cause fan stall.
What wind-loading and structural strength do these stacks offer?
Maya’s FRP stacks are rib-reinforced to handle high wind forces and environmental exposure. Dual finishing enhances surface integrity and weather resistance.
Are there any case studies or proven benefits?
Yes—industry case studies show:
15–30% energy cost savings
Uniform airflow profiles with lower turbulence
Improved static efficiency
How are fan stacks shipped and installed?
They are typically manufactured in modular sections for:
Simplified shipping
Quick on-site assembly
May include extras like access doors, inspection openings, and custom colors.
What is a fan casing and why is it important?
A fan casing (or fan housing) is the outer shell that encloses the fan blades. Its main purpose is to direct airflow efficiently, maintain structural support, and ensure safe operation by preventing contact with moving blades. A well-designed casing minimizes leaks and losses, boosting overall fan system efficiency.
What does a fan cylinder do in a cooling tower or ACC?
A fan cylinder is the cylindrical section that surrounds the fan blade tips, guiding airflow and maintaining a tight clearance. This ensures that air passes through the blades with minimal tip leakage. A precise fan cylinder reduces power loss, prevents recirculation, and maximizes the fan’s static efficiency.
How is a fan ring different from a fan cylinder?
The fan ring usually refers to the inlet or the flared part (inlet bell) of the assembly. It smooths incoming airflow into the fan, lowering turbulence and noise. The fan ring’s aerodynamic shape helps achieve a more uniform air velocity profile, which improves the fan’s performance and lowers energy consumption.
What is a fan shroud and how does it benefit performance?
A fan shroud is an extension that encloses the fan blade tips and helps channel air through a confined path. In automotive cooling or HVAC, it ensures that all air pulled by the fan moves through the radiator or heat exchanger, avoiding bypass. In industrial cooling towers, a shroud acts like a diffuser or cone, helping recover velocity pressure for better static pressure recovery.
Where can I find technical standards or comparisons for fan stacks?
Few important calculations of “Fan Stacks”
Pressure Recovery By Fan diffuser :
Effect of inlet shape on Dynamic Pressure